Thermal transfer technology refers to the use of special metal hot stamping plates to transfer hot stamping foil to the surface of the printing material by means of heating and pressure.
The advantages of thermal transfer technology mainly include the following points.
(1) Good quality, high precision, clear and sharp edges of hot stamping images.
(2) The surface gloss is high, and the hot stamping pattern is bright and smooth.
(3) Wide selection of hot stamping foils, such as hot stamping foils of different colors, hot stamping foils with different gloss effects, and hot stamping foils suitable for different substrates.
(4) Another outstanding advantage of the thermal transfer process is that it can be used for three-dimensional hot stamping. The computer-controlled numerical control engraving and plate-making (CNC) method is used to make a three-dimensional hot stamping plate, so that the graphics and text processed by the hot stamping have a clear three-dimensional level, forming a relief effect on the surface of the printed matter, and generating a strong visual impact effect. Three-dimensional hot stamping can make the packaging have a unique touch.
It is precisely because the thermal transfer process has many of the above-mentioned advantages, it is favored by the majority of users and consumers, and is widely used. However, the thermal transfer process requires special equipment, a heating device, and a hot stamping plate. Therefore, obtaining a high-quality hot stamping effect also means paying a higher cost.
Use special thermal transfer ink to print various patterns on a special kind of paper, and then transfer the patterns to the product through temperature and pressure. This special paper in the thermal transfer process is called thermal transfer paper. Transfer printing refers to the printing process in which dye is transferred to fabric via transfer paper. It is based on the sublimation characteristics of some disperse dyes, selects the disperse dyes sublimated at 150 ~ 230 ° C, mixes it with the paste to make "color ink", and then prints the "color ink" to different design patterns. Transfer paper (this is a special paper, so it is called transfer paper), and then closely transfer the printed paper with the pattern to the fabric, and enter the fabric after diffusion under the control of a certain temperature, pressure and time Internally, to achieve the purpose of coloring.
Thermal transfer method:
1. Sublimation method This is the most commonly used method, using the sublimation characteristics of disperse dyes, using disperse dyes with molecular weights of 250 to 400 and particle diameters of 0.2 to 2 microns and water-soluble carriers (such as sodium alginate) or alcohol-soluble carriers ( Such as ethyl cellulose), oil-soluble resin made of ink, processed on a transfer printing machine at 200 ~ 230 ° C for 20 ~ 30 seconds, so that the disperse dye is transferred to polyester and other synthetic fibers and fixed.
2. The dye in the ink layer of the transfer paper is selected according to the nature of the fiber. The fabric is first paddled with a mixed solution consisting of fixing aids and pastes, and then moved by hot pressing in a wet state to transfer the dye from the transfer printing paper to the fabric and fix it. Finally, it is steamed and washed Wait for wet treatment. When the dye is transferred, a greater pressure is required between the fabric and the transfer paper.
3. The ink layer of the transfer paper of the melting method uses dye and wax as the basic components. By melting and pressing, the ink layer is embedded in the fabric so that part of the ink is transferred to the fiber, and then the corresponding post-treatment is performed according to the nature of the dye. When the melting method is used, a larger pressure is required, and the transfer rate of the dye increases as the pressure increases.
4. The ink layer peeling method uses ink that can produce strong adhesion to the fiber after being heated. Under a small pressure, the entire ink layer can be transferred from the transfer paper to the fabric, and then the corresponding fixing treatment can be performed according to the nature of the dye. .
Sublimation transfer printing process
The various styles, colors, patterns and patterns required by the customer are printed out by computer design-computer color separation-electro-engraving platemaking-wheel gravure printing heat transfer paper-heat transfer processing to polyester chemical fiber fabric, TC cloth, long pile fabric , Artificial leather and other different materials, this process printing is more traditional silk screen and dye printing, in the richness of pattern fancy, the clarity of the layer, the color is bright, the degree of fidelity and environmental protection, washable, lightfast and feel All aspects have been greatly improved. It is a popular printing and dyeing process that is highly respected in the world and the products are becoming high-grade!
Sublimation transfer printing principle
The sublimation method uses the sublimation characteristics of disperse dyes, using disperse dyes with molecular weights of 250 to 400 and particle diameters of 0.2 to 2 microns, water-soluble carriers (such as sodium alginate) or alcohol-soluble carriers (such as ethyl cellulose), oil The ink is made of soluble resin and processed on a transfer printing machine at 200 ~ 230 ° C for 20 ~ 30 seconds to transfer and fix the disperse dye to synthetic fibers such as polyester. The sublimation method generally undergoes three processes: before the transfer process occurs, all the dyes are in the printed film on the paper, the dye concentration in the printed fabric and the air gap is zero, and the size of the air gap depends on the fabric structure and yarn count And the transfer pressure; during the transfer process, when the paper reaches the transfer temperature, the dye begins to volatilize or sublime, and forms a concentration of volatilization between the paper and the fiber. When the printed fabric reaches the transfer temperature, the dye adsorption starts on the fiber surface until A certain saturation value is reached. Since the transfer of dye from paper to fiber is continuous, its rate of adsorption depends on the rate at which the dye diffuses into the fiber. In order to allow the directional diffusion of the dye, vacuum is often drawn under the bottom of the dyed object to achieve the directional diffusion transfer of the dye; after the transfer process, after the dyed object is colored, the dye content on the paper decreases, and some of the remaining dye migrates to Inside the paper, the amount of residual dye depends on the vapor pressure of the dye, the affinity of the dye for the pulp or transfer paper, and the thickness of the printed film. The sublimation method generally does not need to undergo wet treatment, which can save energy and reduce the load of sewage treatment.
Transfer printing is not only suitable for synthetic fiber fabrics, but also for the printing of natural fiber pure spinning and its blended fabrics. It has the following advantages:
(1) No water and no sewage;
(2) The process flow is short, and it is the finished product after printing, without post-treatment processes such as steaming and washing;
(3) Fine patterns, rich and clear layers, high artistry and strong three-dimensional sense, which are beyond the common methods of printing, and can print photography and painting style patterns;
(4) The color of the printing is bright. During the sublimation process, the tar in the dye is left on the transfer paper without contaminating the fabric;
(5) The authenticity rate is high, and multiple sets of color patterns can be printed at one time during transfer without the need to match flowers;
(6) Strong flexibility, customers can print it in a short time after selecting the pattern.
The main application of thermal transfer
1. Clothing transfer fabric, curtain fabric, sand release, umbrella fabric, handbag, carpet fabric, toy fabric and other heat transfer printing
2. High temperature resistant plastic material or plastic material surface treated by spraying, baking paint, electrophoresis, etc. Thermal transfer decoration 3. Metal decorative board, anti-theft door, metal molded door, aluminum profile after spraying, baking paint, electrophoresis , Metal ceilings, curtain rails, metal round tubes, handicrafts, hardware furniture and other metal surface thermal transfer decoration.
4. 1. The front and back of various natural leathers. 2. PU or PVC surface, such as fabric coated with PU or PVC.
Welcome to surf our luxury paper packages.We are good at manufacturing the shoes box.
OUR company offers a variety of children's shoes boxes, covering children from different manufacturers shoebox pictures, pictures of different types of children's shoebox, user select appropriate child shoebox through product detail.
As you can see,this krown box materials are high quality kraft paper without any printing.It is the plane structure box and with the has the strong hardness for packing the shoes ans protect the shoes.Its size is 190x150x80mm.It is nice for baby shose displaying.
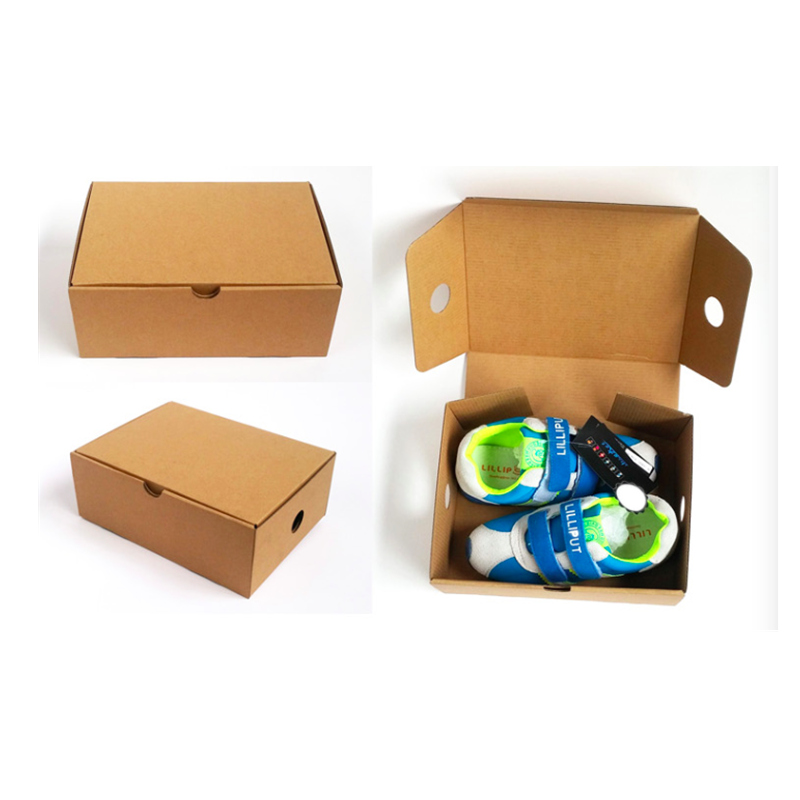
The box size is suitable for the children's shoes. The perfect material and hardness is good enough defend the shoes from damages when they wre transported.This kind of shoes box can bring the good protetation for the shoes.
It has the nice die cuts and perfect tightness for transportation.
We have many years experience for producing the paper boxes.Welcome to our childrens' shoes box trip!Wish you have a nice trip!
Clear Plastic Children Shoe Box,Small Packaging Children Shoes Box,Cardboard Children Shoe Box
Shenzhen Haotuanyuan International Trading Co.,Ltd , https://www.luxurypaperbox.com