Editor's note: In printing, the phenomenon of uneven ink color is one of the common drawbacks. Inhomogeneous ink is characterized by inhomogeneity of the ink on the entire sheet, that is, the deep part is not deep, but the light part is not light, and sometimes it is bar-shaped, sometimes into a sheet, sometimes in a dotted shape. There are many. There are many reasons for these problems, so it is very important to control the ink process during the printing process while finding the crux.
In fact, printing ink instability with ink itself has a great relationship, such as the deployment of ink viscosity ah ah, and so on. As a result, the topic of this issue will be based on the original contents of the previous issues and will talk about the ink of printed products.
â– Test of ink effect of printed products
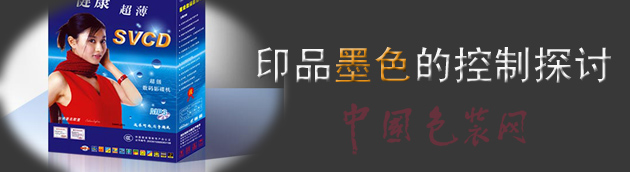
Normal > Offset Ink Measurement and Adjustment Technology Innovation
Normal > Interpretation of " Text Ink " Technical Indicators ( 1 ) ( 2 )
Normal > Overprinting of color prints
Normal > ZMD2 text ink meter special measuring instrument
â– The reason that affects the ink color unevenness
The visual effect of printed ink is one of the important factors to measure the quality of printed matter. The following are the conditions that directly affect the ink color of printed products.
(1) The effect of printing ink layer thickness and viscosity on ink color
The moderate printing ink layer is an important measure to ensure the quality of the printed ink and to prevent the print from sticking. If the ink layer is thicker, its viscosity will inevitably increase, and it will easily lead to paper pull, which will affect the evenness of the printed ink. If the printing ink layer is thin and the ink viscosity is insufficient, the printed ink will be too light, and the visual effect of the printed product is also Just bad. As the printer's rotation time increases or the printing speed increases, the friction coefficient increases, and the ink temperature also gradually increases. Therefore, the ink becomes thin and its viscosity decreases accordingly. Therefore, these conditions must be taken into consideration when transferring ink to ensure that a batch of products can obtain a relatively balanced printing ink color. However, in the actual production process, the decrease of the ink viscosity is unavoidable, and the ink is often dark at the beginning of the printing process and fades afterwards. This can be achieved by appropriately adjusting the rotation angle of the ink transfer roller. The amount of ink keeps the shades of ink before and after. In addition, in order to prevent the ink viscosity variation from being too severe and affect the balance of ink color, the contact between each roller and the iron roller should not be too tight, and the glue should not be too hard to minimize frictional heat and keep the ink properly. concentration.
(2) The effect of printing pressure on ink color
Printing pressure is one of the important conditions for imprint transfer. Since the surface of the printing plate is not absolutely flat, the surface of the paper will inevitably contain slight irregularities and uneven thickness. If the printing pressure is insufficient or uneven, the printing on the plate will be printed. Ink will inevitably appear uneven. Therefore, the ideal printing process is based on the "three levels" (ie, the plate surface and the ink roller and the lining body are relatively flat to obtain good contact conditions), and the thinner ink layer is used to achieve a balanced printing pressure. , to get a more uniform ink on the print. If the printing pressure is insufficient or uneven, there is a poor contact between the lining body and the printing plate surface. By increasing the amount of ink to be fed, the visual effect of the ink on the printing surface can be satisfied, but this not only increases the consumption of ink, but also occurs easily. Dirty printed products are undesirable.
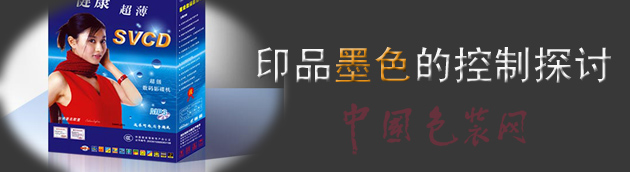
As far as the embossing and peaceful printing process is concerned, whether the printed product can obtain the ideal ink color has a close relationship with the quality of the rubber roller. The equipment for printing color prints is equipped with an ink transfer roller, an ink roller and an ink roller. There are five or six or even more than ten ink meter rollers, of which the ink roller and the ink roller are the most influential factors in the ink shade. The quality of the rubber roller is mainly manifested in the aspects of elasticity, stickiness, roundness, and surface finish, while the main influence on ink density is stickiness. In the printing process, only a certain degree of stickiness of the rubber roller is ensured, so as to ensure that the amount of ink applied to the plate surface is uniform during each printing cycle. However, in the actual production process, the cohesiveness of the rubber roller is not stable. First, due to the increase of paper dust in the ink, the viscosity of the colloid is affected; secondly, the viscosity agent (ie, glycerin) on the surface of the colloid increases with the temperature and the use time. Prolonged and lost, the adhesive surface of the roller gradually reduces the viscosity, the corresponding decline in the ink absorption performance, thus affecting the balance of ink ink. Therefore, the printing plate product should use a more stable quality polyurethane roller. If printing bulk products, clean the rollers at a proper time.
(4) The effect of the difference in paper quality on the ink color of printed products
In fact, the relationship between paper and ink is complicated. If only considering the shade of ink in a book, it should be noted that the smoothness of the paper surface has a certain relationship with ink. If the pressure of each plate is the same, the smoothness of the surface of the paper is inversely proportional to the consumption of ink, and the amount of ink sucked by the sleek lover is small, and vice versa. Therefore, if there is a difference in the smoothness of the positive and negative sides of the paper, the method of increasing the amount of ink and the pressure should be taken as appropriate and appropriate adjustments can be made. The printing is used to print glossy first, and when the rough surface is printed, the amount of ink is properly increased to achieve a good printing effect.
(5) The effect of light changes on ink color of printed products
Vdisplay is a professional promotional display supplier in China. We offer Customized high quality Clothing Displays,OEM Apparel Display Stands.With More than 20 years in Promotional Display industrial ,We very much experience in design and manufacturing Clothing Display Racks,MDF Shoe Display Stands,Metal Socks Display Racks,Apparel Display Stands ,Garment Display Stand.
We have been offering a superior range of Shoe Display Racks. These shoe display racks offered by us are widely acclaimed among the patrons for their high storage capacity, strength, attractive designs, tear resistance and elevated durability.
Shoe Display Rack,Shoes Display Shelves,Shoe Display,Shoe Display Shelves
Vista Display Stand Co., Ltd. , http://www.vistadisplayfixture.com